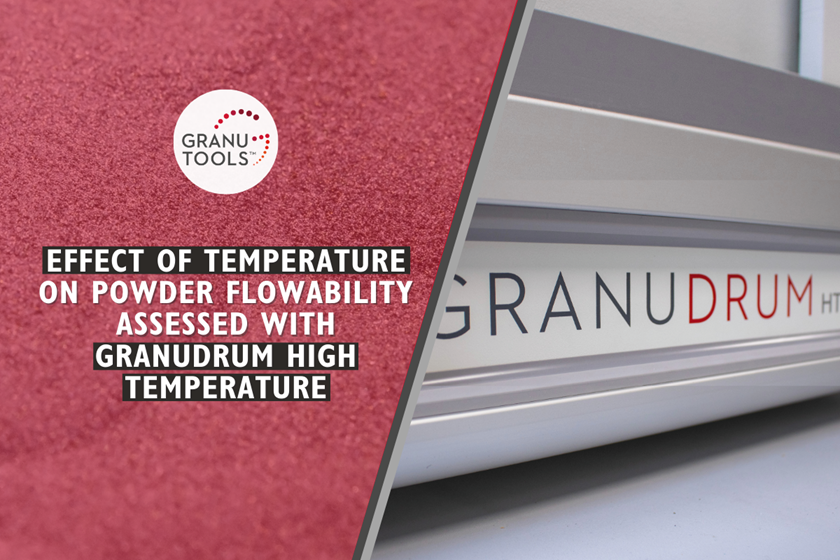
Application notes
Effect of temperature on powder flowability assessed with GranuDrum HT
Learn more about the impact of temperature on powder cohesion thanks to the temperature control of the GranuDrum High Temperature instrument.
Introduction
Numerous applications involve processing granular materials or powders at elevated temperatures. This can be due to requirements of the process or variations of the environmental conditions especially for production sites located around the world. Temperature elevation can induce different mechanisms that will change the powder properties such as moisture evaporation, change in particle properties (stiffness, shape roughness,…), or can induce oxidation… These modifications in the powder change the powder's cohesiveness which impacts its flowability [1]. Therefore, powder flowability must be evaluated as much as possible at a temperature close to the one in the process to provide reliable predictions.
In this study, we investigated the influence of temperature on three different powders generally used in powder bed fusion processes for Additive Manufacturing (AM) and on one powder blend generally used for dry coating processes in battery production. In AM, the powder is usually spread at a high temperature to form a powder bed layer, close to the sintering temperature, and then a laser or a plasma beam sinters or melts the powder at precise regions to print the part layer after layer. For battery production, electrodes are created in dry processes by conveying a blend of different powder materials in hot conditions into a calendar gap to generate a thin film. One of these materials, called a binder, consisting of plasticizing material gives the global flow properties of the powder blend and is sensitive to temperature. Therefore, it is important to perform measurements at a temperature close to the process to predict the flowability. The flowability and the rheology of the powders are evaluated in a rotating drum geometry (GranuDrum HT). The Dynamic Cohesive Index metric computed by the instrument [2] is used to evaluate the influence of temperature on the cohesive behavior of the materials.
On the one hand, the Dynamic Cohesive Index allows to quantify powder flowability. The larger this metric the lower the flowability, leading to poor and intermittent flow. For battery production, poor flowability results in an inhomogeneous thickness of a produced film after the calendar gap. On the other hand, this Dynamic Cohesive Index is known to be correlated with powder spreadability in powder bed fusion processes for AM. The larger the Dynamic Cohesive Index the lower the spreadability (ISO/ASTM TR 52952:2023). Therefore, the Dynamic Cohesive Index allows to assess the effect of temperature on flowability and/or spreadability.
Here, a significant impact of the temperature elevation on powder flowability/spreadability is observed. Different effects of the temperature on powder cohesion are observed depending on the investigated material, and attributed to different possible mechanisms.
Powder Materials
In this work, four powder materials were analyzed: three used for AM and one for battery production. For AM the powder tested were: a Polyamide powder (PA11), a Titanium alloy powder (Ti-6Al-4V), Aluminum alloy powder (AlSi10Mg). The tested powder used for dry process in battery production was a blend of Lithium Iron Phosphate (LFP, active material of the battery), Carbon Black (CB, conductive additive), and Polytetrafluoroethylene (PTFE, binder). These powders were selected for their different behaviours with temperature to highlight the importance of characterizing powder at temperatures close to the manufacturing process such as AM for the three first powders or dry process for the powder blend.
GranuDrum High Temperature
The GranuDrum instrument is an automated powder flowability measurement method based on the rotating drum principle. A horizontal cylinder with transparent sidewalls called drum is half filled with the sample of powder. The drum rotates around its axis at an angular velocity ranging from 2 rpm to 60 rpm. A CCD camera takes snapshots (30 to 100 images separated by 1s) for each angular velocity. The air/powder interface is detected on each snapshot with an edge detection algorithm. Afterwards, the average interface position and the fluctuations around this average position are computed. Then, for each rotating speed, the Dynamic Angle of Repose αf is computed from the average interface position, and the Dynamic Cohesive Index (DCI) is measured from the interface fluctuations [2]
Figure 1: Sketch of GranuDrum measurement principle
In general, a low value of the Dynamic Angle of Repose corresponds to good flowability. It is influenced by a wide set of parameters: the friction between the grains, the shape of the grains, the cohesive forces (van der Waals, electrostatic, and capillary forces) between the grains. On the contrary, the Dynamic Cohesive Index is only related to the cohesive forces between the grains. A cohesive powder leads to an intermitted flow while a non-cohesive powder leads to a regular flow. Therefore, a Dynamic Cohesive Index close to zero corresponds to a non-cohesive powder. When the powder cohesiveness increases, the Dynamic Cohesive Index increases accordingly and the spreadability decreases.
The GranuDrum HT operates identically to the GranuDrum with the difference that measurements are performed at a controlled temperature from room up to 250°C.
Figure 2: Picture of the GranuDrum HT (left) with a focus on the heating device (right)
LEARN MORE ABOUT THE GRANUDRUM HT
Dynamic Cohesive Index analysis
Experimental Protocol
The three powders were analyzed with the GranuDrum HT. For each powder, an increasing speed sequence from 2 up to 60 rpm was performed at different temperatures. The curves of the Dynamic Cohesive Index as a function of rotating speed were compared to assess the powder cohesion evolution with temperature and shear rate. In this way, the effect of temperature on powder cohesion and powder rheology can be evaluated.
For polymer powders, the process temperatures for 3D printing must be lower than the melting temperature. For the case of PA11, the melting point is around 180°C and the process temperature is thus lower than this temperature. Therefore, the powder was tested at 80°C, 120°C, and 140°C and at room temperature to assess the evolution of the cohesion with temperature. The metal powders were measured at 200°C and room temperature. For battery electrodes dry processing,blends with PTFE are heated and handled at around 160°C before being poured into a calendar gap at the same temperature. Therefore, the temperature was set at 160°C for the powder blend.
Experimental results and interpretation
Polymer powder (PA11)
In the case of PA11, a significant increase in cohesion is observed with temperature as highlighted by the gradual evolution of the DCI curves. The shear-thinning observed at room temperature is conserved even at higher temperatures. This global increase in cohesion with temperature is important. Indeed, this implies that the spreadability of the powder during the process at high temperatures would be lower than the spreadability predicted by a measurement performed at room temperature. Therefore, it is preferable to characterize the powder at a temperature close to the process to assess correctly its spreadability. For the PA11, this spreadability could be improved by decreasing the temperature during the recoating step. Another possibility would be to increase the speed of the recoater since the shear-thinning behaviour is present at room and high temperatures.
This evolution in DCI may be due to particle sintering or partial melting of the polymer grains. Indeed, in polymer Additive Manufacturing, polymer powders are generally heated and spread close to the melting point (between 180°C and 189°C for PA11) to reduce the energy consumed by the selective laser (or plasma). Therefore, solid bridges can be generated, especially with amorphous materials like polymers, leading to sintering between particles. These solid bridges limit the mobility of particles and thus increase the cohesion of the powder.
Figure 3: Effect of temperature on PA11 cohesion
Titanium alloy
in the case of Titanium alloy, a decrease in cohesion is observed at 200°C compared to room temperature at a low shear rate. Contrary to PA11, heating the Ti-6Al-4V powder has the advantage of reducing the cohesion and thus improving the spreadability during the recoating step. However, this advantage is only available at low shear rates and identical behaviour would be expected at high shear rates independently of the temperature.
This decrease in cohesion may be due to the drying of the capillary bridges, responsible for a cohesive interaction at room temperature. At higher rotating speeds (higher shear rates) the curves are identical, indicating that the powder spreadability is sensitive to humidity essentially at low shear rate.
Figure 4: Effect of temperature on Titanium alloy powder
Aluminum alloy
In the case of Aluminum alloy, a change in the rheology is observed due to temperature. Indeed, the shear-thickening observed at room temperature is strengthened at 200°C. It results in a decrease in cohesion with temperature at low shear rates while the contrary is observed at large shear rates. Consequently, if the powder is spread at a low shear rate, the spreadability is expected to be improved with temperature while it is expected to decrease with temperature if the spread is done at a high shear rate. In addition, this highlights the importance of characterizing the powder rheology and the effect of temperature on it. For this case, the spreadability during the recoating step at high temperature is more sensitive to shear rate than what can be predicted by a measurement performed at room temperature.
Complex mechanisms could explain the strengthening of the shear-thickening for the Aluminum alloy powder. Changes in the surface properties of the particles like stiffness, shape, roughness, or oxidation may be in cause.
Figure 5: Effect of temperature on Aluminum alloy powder
Powder blend for battery
PTFE is a binder consisting of agglomerated polymer chains that can be fibrillated, i.e. deagglomerated by a dedicated process, to obtain long chains that tangle with LFP and CB particles and give the ‘’plastic’’ behaviour of the whole material. Although representing a few percent in the blend, it highly determines the flow behaviour of the blend. Here, different evolutions with temperature are seen depending on the level of fibrillation of the powder. Indeed, for the not fibrillated powder, an increase in Dynamic Cohesive Index is seen with temperature only for intermediate shear rates, corresponding to rotating speeds between 10 and 40 rpm. The flowability is thus expected to be reduced at intermediate shear rates while it remains unchanged at low or large shear rates. On the contrary, the temperature increases the Dynamic Cohesive Index from low to high shear rates of the fully fibrillated blend. In addition, the difference in Dynamic Cohesive Index is the largest at high rotating speed while no significant difference was obtained for the not fibrillated powder beyond 40 rpm. Therefore, depending on the level of fibrillation of the powder and the undergone shear rate during the process, small or large differences in flowability can be expected with temperature.
This difference in sensitivity with temperature may come from the difference in network between the fibrillated powder and the not fibrillated powder. Indeed, for the first, LFP and CB particles are connected and tangled with PTFE while for the second one has a granular material of individual particles with agglomerated chains of PTFE. PTFE is a polymer material sensitive to temperature. The way temperature influences the interplay between this material and the other particles probably depends on the existing network between PTFE and the other particles and may explain such differences in behaviour with temperature.
Figure 6: Effect of temperature on powder blend of LFP, CB and PTFE
Conclusions
In this study, the impact of temperature on powder cohesion is clearly evidenced thanks to the temperature control of the GranuDrum HT. Four different powders were investigated and various behaviours were observed with temperature depending on the tested powder:
- The temperature can induce partial melting or sintering between particles, increasing the cohesion, especially in the case of polymer powders. → example of PA11
- The temperature can induce a drying of the powder, decreasing the cohesion coming from the capillary bridges. → example of Ti-6Al-4V
- The temperature can induce a change in the rheology of the powder due to a change in particle properties (shape, stiffness, oxidation,…). → example of AlSi10Mg
- The temperature sensitivity can depend on the structure inside the powder leading to different changes in flowability with temperature. → example of LFP+CB+PTFE blend fibrillated or not
These changes in powder cohesion change the flowability of the powder and consequently affect the quality of the final product due to a change in processability. As a result, characterizing a powder at room conditions while the manufacturing process is done at an elevated temperature can lead to wrong conclusions. Therefore, it is of huge importance to characterize powder properties at a temperature close to the process for a better processability assessment. For this purpose, the GranuDrum HT technology opens the way to flowability assessment, integrating the temperature as a control parameter, for Additive Manufacturing, dry processes for battery production, and many other applications.
LEARN MORE ABOUT THE GRANUDRUM HT
References
- G. Lumay, F. Francqui, C. Detrembleur, N. Vandewalle, Influence of temperature on the packing dynamics of polymer powders, Advanced Powder Technology (2020), 4428-4435, 31(10).
- A. Neveu, F. Francqui, G. Lumay, Measuring powder flow properties in a rotating drum, Measurement 200 (2022), 111548.
- O. K. Radchenko, K. O. Gogaev, Requirements for Metal and Alloy Powders for 3D Printing (Review), Powder Metallurgy and Metal Ceramics (2022), 135-154, 61.