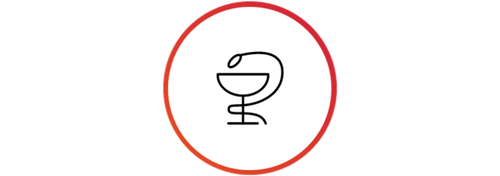
Papers
Flowability of Lactose Powders to Optimise Tableting Processes - 2020
A. Neveu, P. Janssen; G. Lumay, ONdrugDelivery Magazine, Issue 109 (July 2020), pp 58–62
The processability of pharmaceutical powder plays a key role in the design and improvement of production processes for oral delivery systems (e.g. tableting, capsule filling). To control and optimise processing methods, material properties and the behaviour of bulk powder should be characterised. Blending is one of the first steps in a direct compression process and is critical to achieve a homogeneous blend with uniform API loading. Good flow combined with density supports de-agglomeration of an API during blending. Free-flowing powder has a relatively flat powder bed in a blender and tends to set up a “rolling” motion inside the powder bed. This results in ball milling of the API agglomerates, which is beneficial for the uniform spread of the API particles over the blend. Poor-flowing powder has a higher dynamic angle of repose and tends to avalanche. This results in less motion inside the powder bed and less ball milling of agglomerates. De-agglomeration of the API is beneficial to achieve good content uniformity in a pharmaceutical formulation, and this becomes more critical with a lower API dose. Moreover, good flowing properties of a powder are also required for flow through the tableting system, resulting in uniform flow into the die cavities. Insufficient flow can lead to uneven filling of the dies, resulting in large weight and dosage variations of the final tablets. At high tableting speeds, the time to fill dies is reduced, making flow properties of the blend even more important. The particle properties, mainly size and shape, strongly influence the flowability of the powder and thus the critical filling velocity achievable in die filling. Consistent flow is also important for continuous manufacturing processes, which are gaining more and more interest from the pharmaceutical industry. Raw material feeding is usually one of the first units of operation in a continuous manufacturing line. The ability to feed powder consistently and continuously is regarded as one of the critical requirements for finished product quality and therefore stringent control on feeding is required. Lactose is one of the most widely used excipients in the pharmaceutical industry. There are many reasons for its popularity, the fact that lactose is largely inert, relatively inexpensive, safe, many different grades are available and it has a long history of usage in successful formulations worldwide. For direct compression processes such as tableting, lactose excipients can be used as a filler-binder to provide bulk density, compaction and flow to the formulation. Good flow of a pharmaceutical formulation is critical to produce uniform dosage forms. In this article, we present how new measurement methods can help to gain a better understanding of the flowability of lactose powders, which is a necessary step for future improvement of oral delivery systems. Firstly, the well-known angle of repose is estimated to get a first screening of the cohesiveness of the powders. These results are then compared and extended to a vertical flow through an aperture, in a geometry closer to those encountered in die filling. Then, the effect of the process speed on the flowability – i.e. the rheological behaviour – is investigated with the rotating drum measurement method.