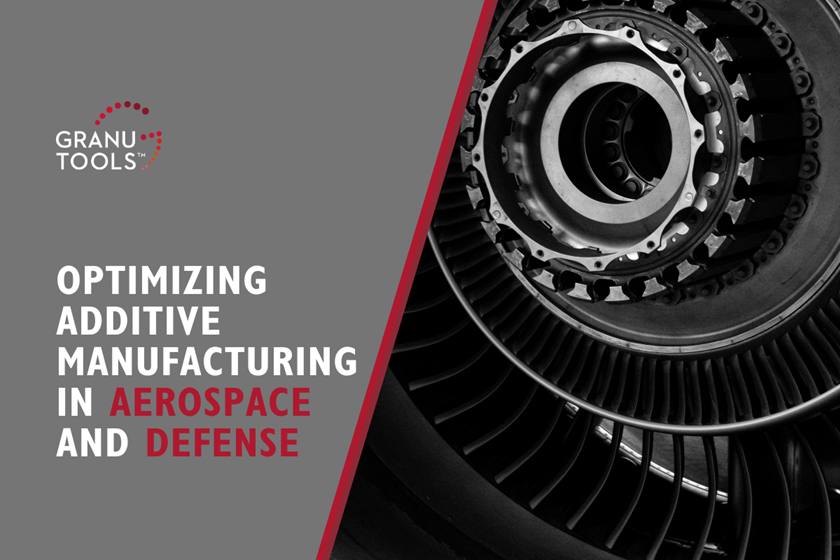
Blog
Optimizing Additive Manufacturing in Aerospace and Defense: The Role of Granutools in Advancing R&D and New Material Development
In the rapidly evolving sectors of aerospace and defense, the integration of advanced technologies is paramount. Additive Manufacturing, commonly known as 3D printing, has emerged as a transformative force, enabling the production of complex components with unprecedented precision and efficiency.
Central to the success of AM processes is the meticulous characterization of powders, the foundational materials in these manufacturing techniques. At Granutools, we offer solutions that significantly enhance Research & Development (R&D) efforts and the development of new materials in these critical industries.
The Imperative of Powder Characterization in Aerospace and Defense
In aerospace and defense, the stakes are exceptionally high. Components must withstand extreme conditions, from the vacuum of space to the rigors of combat environments. AM allows for the creation of lightweight, durable parts essential for modern aircraft, spacecraft, and defense systems. However, the quality of these parts is intrinsically linked to the properties of the powders used. Variables such as flowability, cohesiveness, and packing density directly influence the integrity and performance of the final product.
Granutools: Pioneering Precision in Powder Characterization
Granutools addresses these challenges by providing state-of-the-art instruments designed to analyze and optimize powder properties:
- GranuDrum: This automated powder tester evaluates the cohesion within powders using the rotating drum principle. By analyzing how powders behave under different rotational speeds, GranuDrum provides insights into their flowability and cohesiveness, crucial for ensuring consistent layering in AM processes.
- GranuPack: An advanced tapped density measurement instrument, GranuPack studies the packing dynamics of powders. Understanding how powders compact under tapping is vital for achieving uniform density in manufactured components, directly impacting their mechanical properties.
- GranuCharge: This instrument measures the electrostatic properties of powders, which can affect flowability and handling. In AM, uncontrolled electrostatic charges can lead to uneven powder distribution, compromising the quality of the final product. GranuCharge helps in identifying and mitigating these issues.
Enhancing R&D and New Material Development
For R&D departments focused on developing new materials, Granutools' instruments are invaluable. They enable researchers to:
- Characterize Novel Powders: Accurately assess the behavior of newly developed powders, ensuring they meet the stringent requirements of aerospace and defense applications.
- Optimize AM Processes: Fine-tune printing parameters based on precise powder characteristics, leading to improved component performance and reliability.
- Ensure Quality Control: Maintain consistent powder quality, essential for reproducible AM outcomes, by monitoring properties such as flowability and density.
Real-World Applications and Collaborations
Granutools' impact extends beyond instrumentation; we actively collaborate with industry leaders to advance AM technologies:
- Technical Reports: we contribute to the development of technical reports, such as the ISO/ASTM TR 52952:2023, focusing on the characterization and optimization of metallic powders used in powder bed fusion and binder jetting processes.
- Case Studies: Through detailed case studies, we demonstrate how our instruments can measure the flowability of powders used in additive manufacturing, providing valuable insights for process optimization.
Conclusion
In the high-stakes sectors of aerospace and defense, precision and reliability are non-negotiable. Granutools equips these industries with the tools necessary to thoroughly understand and optimize powder characteristics, thereby enhancing the efficacy of additive manufacturing processes. By integrating Granutools' instruments into their R&D and production workflows, organizations can confidently innovate and develop new materials, ensuring that they meet the exacting standards required for critical applications.